3. Assess realistic final-customer demand lead times and inventory levels as an early-warning 3. and respond to (or, where possible, contain) system for interruption and establish a recovery shortage-buying behavior of customers. plan for critical suppliers by commodity. 4. In situations in which tier-one suppliers do not 4. Optimize production and distribution capacity to ensure employee safety, such as by supplying have visibility into their own supply chains or are personal protective equipment (PPE) and not forthcoming with data on them, companies can engaging with communication teams to share form a hypothesis on this risk by triangulating from infection-risk levels and work-from-home a range of information sources, including facility options. These steps will enable leaders to exposure by industry and parts category, shipment understand current and projected capacity impacts, and export levels across countries and levels in both workforce and materials. regions. Business-data providers have databases that can be purchased and used to perform this 5. triangulation. Advanced-analytics approaches 5. Identify and secure logistics capacity, estimating capacity and accelerating, where possible, and network mapping can be used to cull useful and being flexible on transportation mode, information from these databases rapidly and when required. highlight the most critical lower-tier suppliers. 6. Combining these hypotheses with the knowledge 6. Manage cash and net working capital by running stress tests to understand where supply-chain of where components are traditionally sourced issues will start to cause a financial impact. will create a supplier-risk assessment, which can shape discussions with tier-one suppliers. In the following sections, we explore each of these This can be supplemented with the described six sets of issues. outside-in analysis, using various data sources, to identify possible tier-two and onward suppliers in Create transparency affected regions. Creating a transparent view of a multitier supply chain begins with determining the critical For risks that could stop or significantly slow components for your operations. Working with production lines—or significantly increase cost of operations and production teams to review your bills operations—businesses can identify alternative of materials (BOMs) and catalog components will suppliers, where possible, in terms of qualifications identify the ones that are sourced from high-risk outside severely affected regions. Companies will areas and lack ready substitutes. A risk index for need to recognize that differences in local policy each BOM commodity, based on uniqueness and (for example, changing travel restrictions and location of suppliers, will help identify those parts at government guidance on distancing requirements) highest risk. can have a major impact on the need for (and availability of) other options. If alternative suppliers Once the critical components have been identified, are unavailable, businesses can work closely with companies can then assess the risk of interruption affected tier-one organizations to address the from tier-two and onward suppliers. This stage of risk collaboratively. Understanding the specific planning should include asking direct questions of exposure across the multitier supply chain should tier-one organizations about who and where their allow for a faster restart after the crisis. suppliers are and creating information-sharing agreements to determine any disruption being faced Estimate available inventory in tier-two and beyond organizations. Manufacturers Most businesses would be surprised by how much should engage with all of their suppliers, across all inventory sits in their value chains and should tiers, to form a series of joint agreements to monitor estimate how much of it, including spare parts and Supply-chain recovery in coronavirus times—plan for now and the future 77
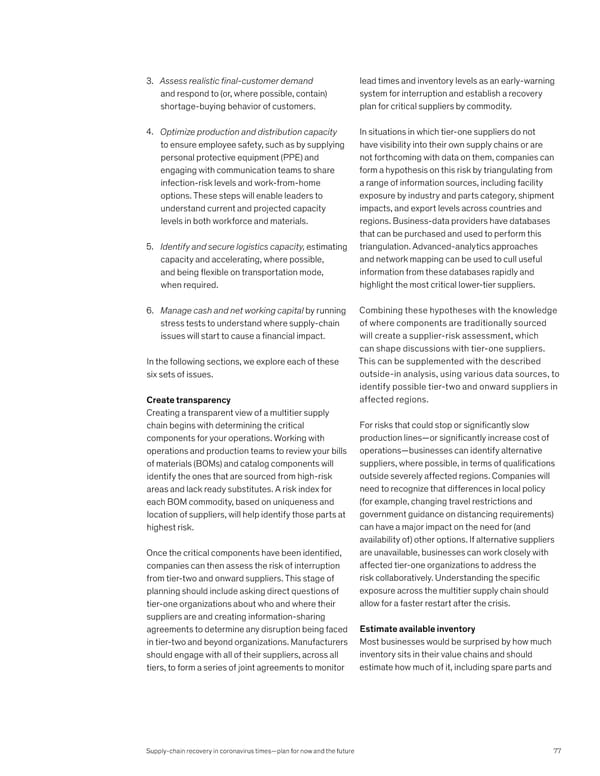