story illustrates the new organization paradigm: The argument for more flexible and shorter supply empowerment and speed, even—or especially— chains has been building for years. In 2004, an when information is patchy. article in the McKinsey Quarterly noted that it can be better to ship goods “500 feet in 24 hours [rather Another is to think of ecosystems (that is, how all than] shipping them 5,000 miles across logistical the parts fit together) rather than separate units. and political boundaries in 25 days … offshoring Companies with healthy ecosystems of suppliers, often isn’t the right strategy for companies whose partners, vendors, and committed customers can competitive advantage comes from speed and a find ways to work together during and after times of track record of reliability.”1 crisis because those are relationships built on trust, not only transactions. Start redesigning supply chains to optimize resilience and speed Finally, agility is just a word if it isn’t grounded in Instead of asking whether to onshore or offshore the discipline of data. Companies need to create or production, the starting point should be the accelerate their analytics capabilities to provide the question, “How can we forge a supply chain that basis for answers—and, perhaps as important, allow creates the most value?” That will often lead to them to ask the right questions. This also requires an answer that involves neither offshoring nor reskilling employees to take advantage of those onshoring but rather “multishoring”—and with it, the capabilities: an organization that is always learning reduction of risk by avoiding being dependent on is always improving. any single source of supply. Speed still matters, particularly in areas in which 3. From just-in-time to just-in-time consumer preferences change quickly. Yet even and just-in-case supply chains in fashion, in which that is very much the case, the need for greater resilience is clear. In a survey Stop optimizing supply chains based on conducted in cooperation with Sourcing Journal individual component cost and depending on a subscribers, McKinsey found that most fashion- single supply source for critical materials sourcing executives reported that their suppliers The coronavirus crisis has demonstrated the wouldn’t be able to deliver all their orders for the vulnerability of the old supply-chain model, with second quarter of 2020. To get faster means companies finding their operations abruptly adopting new digital-planning and supplier-risk- halted because a single factory had to shut down. management tools to create greater visibility Companies learned the hard way that individual and capacity, capability, inventory, demand, and transaction costs don’t matter nearly as much risk across the value chain. Doing so enables as end-to-end value optimization—an idea that companies to react well to changes in supply or includes resilience and efficiency, as well as cost. demand conditions. The argument for more flexible and shorter supply chains has been building for years. 1 Ronald C. Ritter and Robert A. Sternfels, “When offshore manufacturing doesn’t make sense,” McKinsey Quarterly, 2004 Number 4. 86 What now? Ten actions to emerge stronger in the next normal September 2020
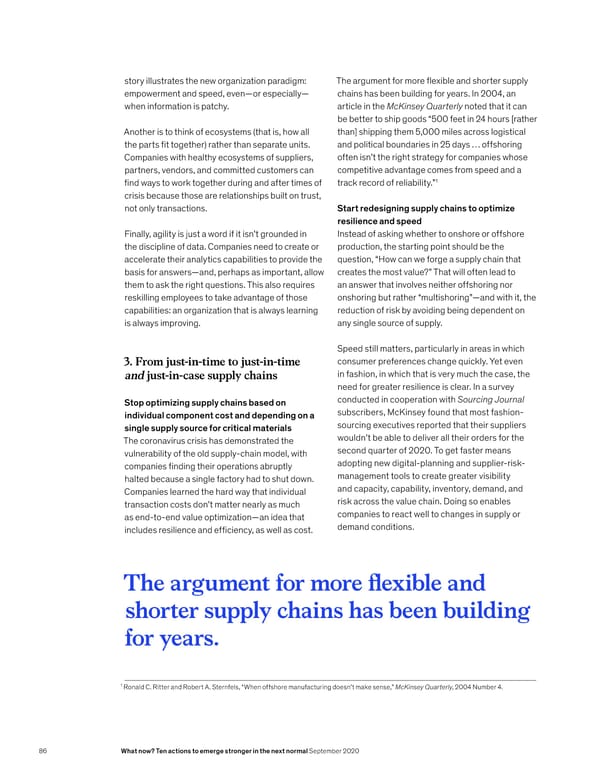